Not just a power play – LPI NZ protects Sky Tower from potentially catastrophic lightning strikes
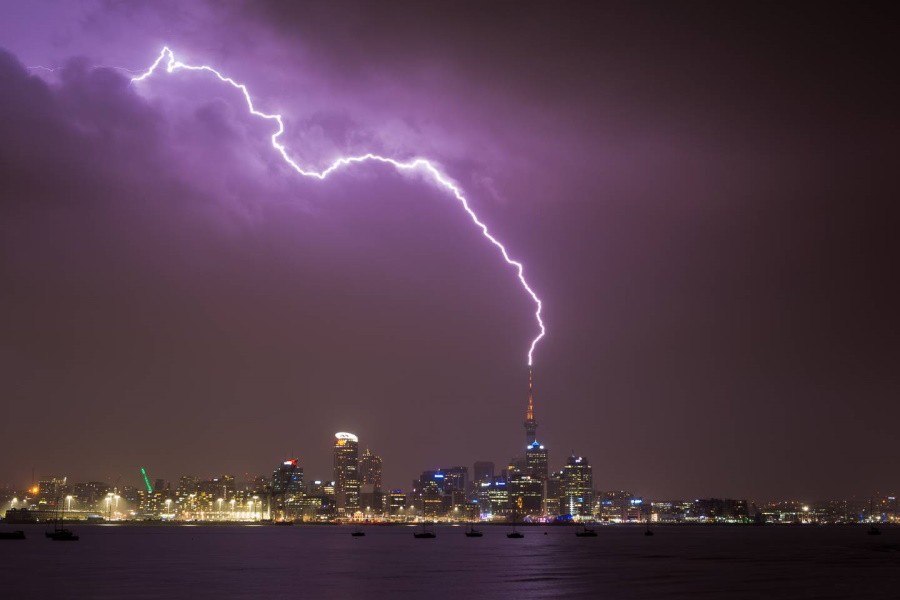
From Rocketlab to the Sky Tower, supermarket chains, hospitals and The Warehouse stores across New Zealand – Lightning Protection New Zealand (LPI NZ) has a rather impressive clientele.
But it’s the reason behind why those customers rely on the team and capabilities of LPI NZ that really shines a spotlight on how important their work is. Because, as the company name suggests, lightning protection is their main service offering, ensuring electrical equipment is safeguarded against lightning strikes and power surges.
Gordan Luetich, Director of LPI NZ, founded the company in 2009, building his business from scratch, and is proud of where he is now. From having to move warehouses numerous times to expand equipment supply, to being involved in some very exciting projects – there’s never a dull day when it comes to protecting some rather significant clients, and their day-to-day operations, from power surges and lightning strikes.
One of LPI’s most recognisable projects sits on top of the tallest building in the southern hemisphere – the Sky Tower. And after 10 years, it’s now time to head back to the Sky Tower to tend to some rather important equipment that requires replacement every decade.
Because of the Sky Tower’s location and height, there are all sorts of communication instruments attached to it, like TV stations, cellular networks and emergency services. And because of its shape, all the cables are attached right next to each other.
“So, if a lightning strike were to hit it and cause damage, it could fry those cables, cause a fire and also result in a power surge for the surrounding infrastructure.” Luetich explained.
In addition to providing lightning protection for its customers, LPI NZ also regularly monitors power supply and quality (Harmonics Mitigation and Power Factor Correction), checking on devices that could be polluting electrical infrastructure, which could in turn lead to overheating and become a serious fire hazard. And considering much of modern society depends on connection to function, there’s a huge potential for failure if equipment, such as data centres and communication networks, were compromised.
Luetich says that while he has seen many changes in the industry over the past 14 years, there aren’t many which have been quite as significant as the roll out of ultra-fast broadband from Chorus.
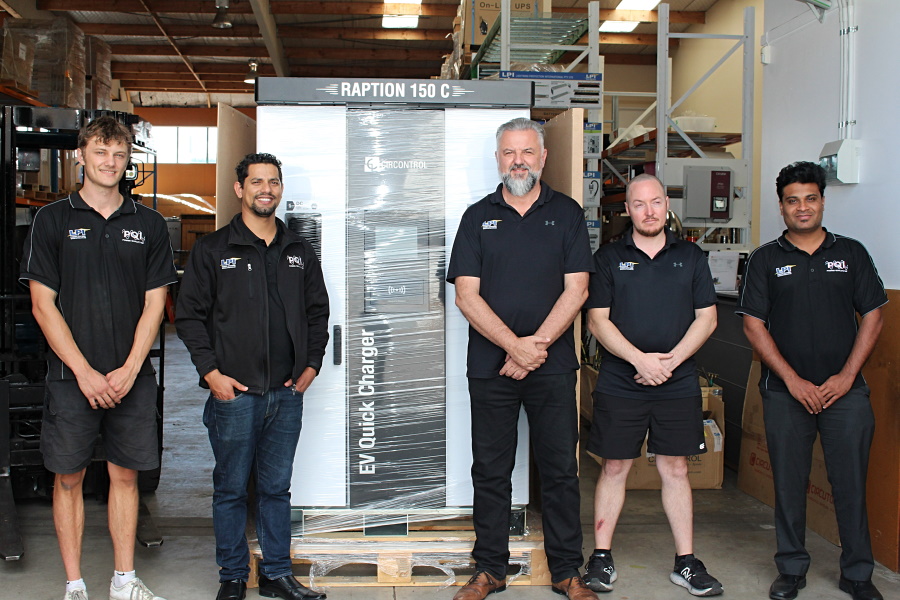
“Of course lightning strikes pose the most serious risk, but monitoring and correcting ongoing power quality for large users of electricity is also critical. And because of fibre broadband, we’ve been able to improve the way we carry out testing and ongoing monitoring of all kinds of electrical equipment.”
For Luetich and his team, the arrival of ultra-fast broadband has meant they can now operate multiple power analysers at one time, whereas prior to fibre it just wasn’t possible for the system to cope with all of the data that needed to be recorded and communicated.
“Around five or so years ago, checking the power quality of a customer meant having to spend a lot of time at their physical locations. But now we are able to install power analysers with a SIM card, then do all the setup from our office via our fibre connection. This set-up capability is in addition to our broadband connection allowing us to stop recording wherever necessary. For example, turning off large chillers in a supermarket and monitoring what happens to the power quality when that happens.
“Our customers can also access this data too, with an alarm to alert them in their own system.”
This has not only been convenient for LPI NZ’s team of engineers but saves their clients the expense of having someone on site for those procedures. And for organisations who require UPS (Uninterrupted Power Supply such as data centres and hospitals), being remotely connected to the client’s network allows for quick and easy access for testing and identifying any potential faults (abnormality in power quality), before they occur. Which, in some cases, could be extremely dangerous.
“As an example, we’re often called upon to install permanent monitoring equipment for non linear equipment loads (like LED lights, VSD, UPS and big video/TV screens). Because of their size, there is a risk of power pollution for such a large electrical appliance, which could overheat the cables and cause a fire or malfunction of the sensitive electrical equipment.”
Fibre also means keeping in touch with overseas operators – in places such as China, Taiwan, Germany, Spain, Croatia, Slovenia and Australia – is a lot more streamlined. Fast fibre minimises the risk of buffering, or interruption to their connection, which is particularly crucial when a technician is needing urgent, on-the-ground assistance from a supplier in Barcelona.
“From checking on inventory remotely to communicating with the sales representatives on the road, and even accessing video tutorials for various equipment, it just makes everyone’s lives so much easier. As we’re getting ready to upgrade the Sky Tower’s lightning protection system, we are able to minimise time required for travelling, parking etc by having our meetings with various consultants online.”
Story by Erin Harrison in partnership with Chorus.